The Environmental Impact Of Using Plastic To Make Microchips
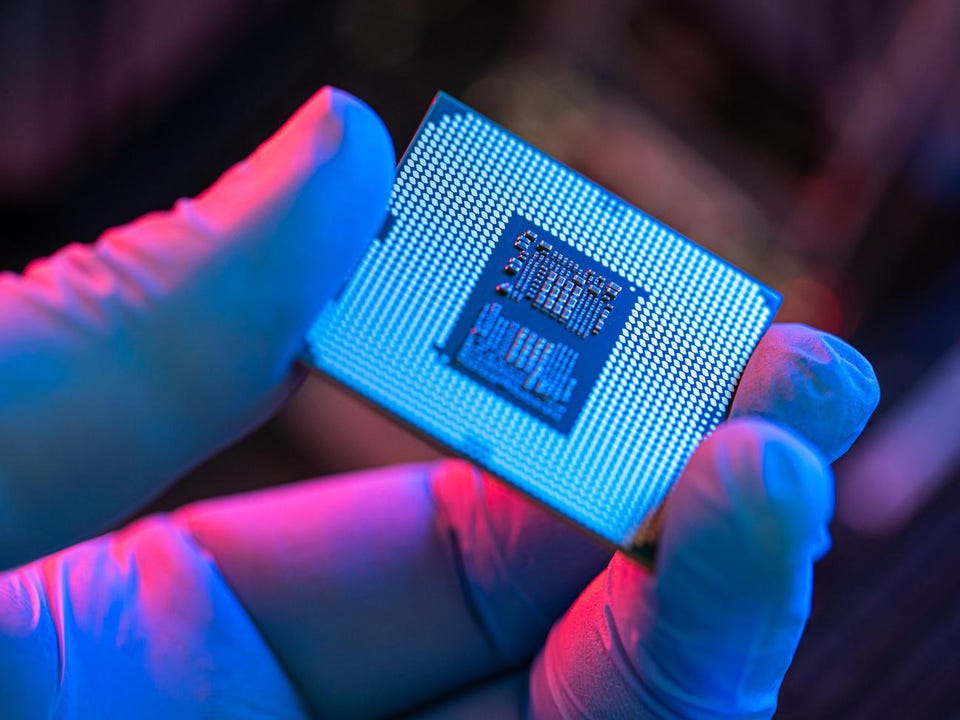
Technology is increasingly touted as the solution to countless environmental challenges, from carbon sequestration to materials recycling. But, as has been widely documented, the silicon chips underpinning these cutting-edge solutions have their own—not insignificant—carbon impact.
So, how do we ensure that technology isn’t creating more carbon than it’s removing? And can plastic chips be part of the solution?
Time For Change
It’s no secret that silicon-based semiconductor production is not particularly environmentally friendly. In addition to using harmful chemicals and gasses such as perfluorocarbons (PFCs), the industry also requires vast amounts of water and energy to get the chips out of the door.
Take Taiwan-based TSMC, for example: As one of the world’s largest semiconductor producers, it naturally has a large energy footprint. In 2020, it announced it was switching to renewable wind energy to limit its environmental impact. But increased energy demand, fuelled by commercial production of its leading-edge three-nanometre chips, exceeded any gains made from green energy; by 2022, its usage was expected to exceed 7% of Taiwan’s total power consumption, more than the city of Taipei.
In fact, the industry as a whole is coming under the spotlight for its prodigious consumption of resources. As global warming affects the water cycle across the planet and flash droughts are predicted to become more frequent, a model that can see a single fab consume millions of liters of water a day clearly needs to change.
A Flexible Alternative To Silicon
Flexible semiconductor technology—flexible integrated circuits (“chips”) based on thin-film transistors—can potentially embody that change. Production of flexible chips omits many of the resource-intensive stages of silicon manufacturing; there are no high-temperature processing steps and far fewer chemical steps. As a result, it uses considerably less power and water than silicon production and significantly reduces the quantity of chemicals and gasses consumed.
Some may be skeptical about the environmental benefits of using plastic. While it’s true that they do use a polymer (read: plastic) substrate, each chip is just microns thick—thinner than a human hair—and typically weighs less than 0.2 mg. For context, 2,000 FlexICs contain less plastic than a single drinking straw.
And as plastics are replaced with more sustainable alternatives, the possibility of biodegradable substrates becomes a tantalizing proposition. In fact, since the substrate is not required for functionality—it simply offers physical support during manufacturing and handling—the flexible chips of the future may eliminate it altogether, reducing their impact to an absolute minimum.
While biodegradable chips are still some way off, their reduced environmental footprint means it still makes sense to use flexible semiconductors wherever possible, saving silicon for those tasks where it’s really needed.
Because silicon technology isn’t going away any time soon. We just need to be sparing in how and where we deploy it.
The Right Tool For The Job
The long lead times and high costs associated with silicon chip design, not to mention the supply chain issues in recent years, have led to overly complex specifications—creating chips that are ready for anything rather than a specific task.
If chips are likely to take months, or even years, to reach production, the thinking goes, they have to be fit for a wide range of use cases, irrespective of immediate need. This effectively results in using a sledgehammer to crack a nut. Because silicon chips deliver high performance at a high cost and with high environmental impact.
Flexible chips deliver “good enough” performance at a fraction of the cost and carbon footprint. This, along with their flexible form factor, means they can be used where it would not be cost-effective—or even possible—to use conventional electronics. It also makes them a compelling alternative to legacy silicon.
As we move from the Internet of Things to the Internet of Everything, tiny, low-cost chips such as these may prove crucial for providing intelligent data and driving efficiency at a low environmental overhead.
A Flexible Revolution
Interest in low-cost, flexible electronics has been accelerating for several years, with a growing ecosystem focusing on various technical approaches. And many of them are looking beyond silicon.
Some are focused on organic semiconductors, which have potential for innovative manufacturing techniques like printing but often have limited performance. At the other end of the spectrum, carbon-based materials, such as carbon nanotubes and graphene, show superior performance but are not yet mature enough for volume production. There are also options, like my company, that use metal oxides that deliver decent performance and for which the manufacturing techniques are effective for high-yield fabrication.
When speaking to potential vendors, ask about your company’s specific use cases and about how the manufacturing capabilities and timeline can meet your specific needs.
A Flexible Future
While the benefits—and market opportunity—of flexible chips have been demonstrated, there are still hurdles to unlocking their full potential.
First, global production capacity must scale to deliver the huge volumes demanded by the market. While some commercial fabs for flexible chips are already in operation, and more are under construction, capacity still lags behind silicon. Over the next decade, significant capital investment is needed to address global demand.
Second, to take full advantage of the opportunities flexible chips present, we need a complete partner ecosystem, just as with silicon. Some elements of this, such as qualified material and equipment suppliers, already exist, but others, such as designers, IP suppliers and assembly partners, need further development.
Finally, we need to find the sweet spot for their application because flexible chips will not replace silicon chips; they’ll complement them. But by using flexible semiconductors for the myriad tasks where “just enough” performance is more than enough, we can free silicon—with its weightier environmental overheads—to tackle the big-ticket items, and help technology to be part of the solution, not part of the problem.