MES And CMMS Are Smarter Together
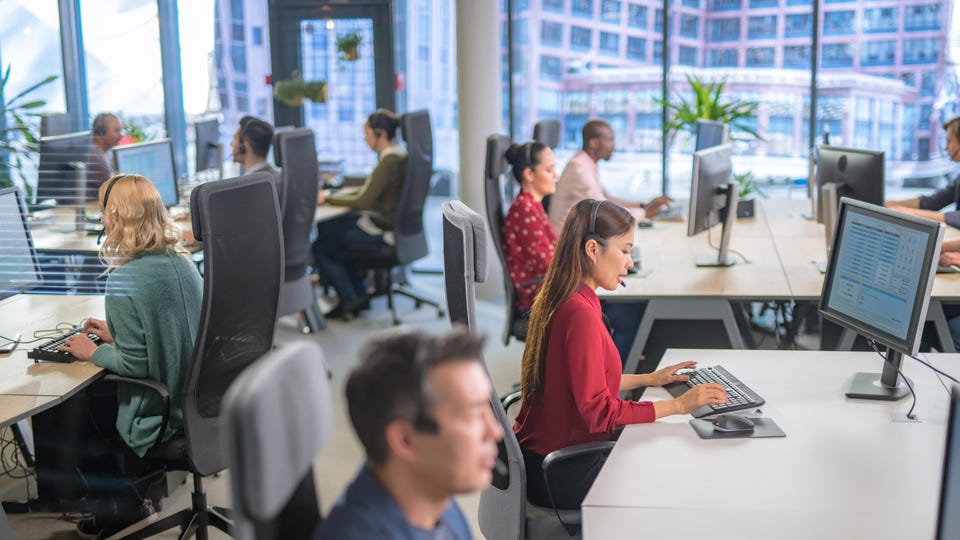
John Clemons consults for Rockwell Automation and Maverick Technologies, a leading platform-independent automation solutions provider.
getty
Smart manufacturing technologies are making a significant impact on manufacturing operations around the world. From the industrial internet of things (IIoT) to artificial intelligence and machine learning, these new technologies are coming together and fueling the benefits of smart manufacturing. While everyone seems to want the newest technology, some older technologies are also having quite an impact on manufacturing.
Manufacturing execution systems (MES) and computerized maintenance management systems (CMMS) have been around for decades and aren’t thought of as the latest in smart manufacturing technologies. But MES and CMMS are just as much a part of today’s smart manufacturing solutions as the IIoT and AI. In fact, today’s MES and CMMS are very sophisticated solutions that have proven themselves over many years, and the impact they’re having on manufacturing continues unabated.
Today’s MES and CMMS embrace the current generation of smart manufacturing technology, including cloud computing, the IIoT, advanced analytics and AI components. The smart aspect of MES and CMMS isn’t just all these smart technologies; it’s the integration of MES and CMMS to create solutions that are far greater than the sum of their parts.
Unified Scheduling
MES and CMMS have always had scheduling capabilities. MES deals with the production schedule and CMMS deals with the maintenance schedule. But that usually means two different schedules for the same equipment. This means conflicts and interruptions with maintenance being interrupted with production demands and production being interrupted with maintenance demands.
With MES and CMMS working together, they create a unified schedule for the shop floor, for both production and maintenance. This is a more streamlined schedule, which makes the shop floor more effective and efficient. It allows for schedule adjustments to be more holistic because everyone can see what’s going on, which makes it much easier to prioritize activities and schedule resources.
Work Instructions
MES and CMMS have always had work instructions. MES work instructions are about how to make the product, run the equipment, perform an assembly, make a batch or execute an inspection. The CMMS work instructions are about equipment maintenance, diagnostics, troubleshooting and repair. This means production and maintenance people must access two different systems just to get the work instructions they need.
With MES and CMMS working together, they create a unified view of work instructions regardless of whether they’re from production, engineering, quality or maintenance. This is especially important for people on the shop floor because programs such as lean manufacturing and autonomous maintenance are blurring the lines between production and maintenance, so there’s rarely a clear delineation of who needs which work instruction. The objective here is to make sure the right person has the right information at the right time without having to worry about what computer system it might come from.
Condition-Based Maintenance
Condition-based maintenance monitors the actual conditions of a piece of equipment to decide what maintenance is needed. Maintenance is only performed when specific indicators show signs of decreasing performance or upcoming failure. Condition-based maintenance is one of the most effective paradigms for executing maintenance activities because it ensures maintenance is only performed when needed.
To make condition-based maintenance a reality, it needs data, often a lot of data, on the equipment, showing the equipment’s status and performance, whether the performance is decreasing, and when a failure of that equipment is predicted. While CMMS executes the condition-based maintenance process, MES collects the data from the equipment, and most importantly, gives the data its context.
The data includes machine cycles, speeds and feeds, temperatures, flows and pressures, vibration and more. The context MES adds includes production order, operation, material, lot number, batch number, product number, product family, crewing information, quality, inspection results and more. With MES and CMMS working together, MES collects the data and CMMS uses that data to determine the condition of the equipment and when maintenance is required.
Equipment Performance
CMMS has always been concerned about the performance of the equipment, usually via metrics such as overall equipment effectiveness (OEE), comprised of availability, performance and quality. But again, it’s MES that collects the data to make the OEE metric truly valuable. MES also adds the context around the OEE metric so that it’s possible to understand not merely the performance trends but the root causes of the performance in terms of orders, products, materials and crews.
Equipment Lifecycle Benefits
The benefits of MES and CMMS working together are clear. They reduce downtime, mean time between failure (MTBF), mean time to repair (MTTR) and operating and maintenance costs, and they increase productivity. Together, they create a seamless solution for the shop floor, providing the right information to the right people at the right time. They collect the required data and schedule the required maintenance, exactly when it’s needed. And they provide the metrics needed to optimize the lifecycle of the shop-floor equipment.
Getting Started
There are a few basic ways to get started. Look for ways to integrate the data so that MES collects data and provides it to CMMS for the maintenance processes. Start with basic downtime data and downtime reason codes to feed into the OEE metric, and then add more data to feed into the condition-based maintenance processes. Don’t start with the entire shop floor. Instead, start with just a few of the most critical, bottleneck machines, and then expand from there. Start small and expand as it makes sense, all the while proving the concepts and, most especially, proving the business value.
MES and CMMS might be decades-old solutions, but they’ve embraced the latest generation of smart manufacturing technology. They’re now a cornerstone to almost any smart manufacturing endeavor just like AI and the IIoT. Together, MES and CMMS provide capabilities that are just not possible with one or the other by themselves. They really are greater than the sum of their parts. MES and CMMS are key elements of how smart manufacturing is transforming the manufacturing industries back into an economic powerhouse.
Forbes Technology Council is an invitation-only community for world-class CIOs, CTOs and technology executives. Do I qualify?